you
for stopping by to learn more about my Twangcaster Proprietary
Bridge design.
For years,
tremolo-style guitar players claimed that their guitars had
different tonal qualities than guitars with fixed-style bridges.
Some claimed it was because of the tremolo block, the tremolo
springs, or a combination of both.
The truth
is, everything mounted onto a guitar will have an impact on
tone. Some things will have a negative effect while others will
be positive. The Twangcaster bridge most definitely has
a positive impact. It does so by reducing the rate of decay
of the tones generated by the vibrating strings, while at the
same time increasing the amplitude of the strings' audible signal.
The Twangcaster
bridge goes beyond simply adding a "tone block" to
the underside of a fixed bridge. Care had to be given to ensure
that the resonate frequency (RF) of the overall bridge was not
in conflict with the RF of the vibrating strings. By choosing
the proper material(s) from which the bridge is milled, and
choosing the ideal profile of the part of the bridge that extends
into the guitar body, the Twangcaster bridge is far superior
to any bridge on the market and will make your T-style guitar
more alive than it has ever been.
|
|
|
|
|
|
The
Twangcaster bridge starts from a solid billet of material.
Shown here is a piece of naval brass. It weighs right at five
pounds (5 lbs) and when completed will weigh a little less than
200 grams.
A
cheaper way of making the Twangcaster bridge would be
to simply screw a tone block to the underside of a fixed bridge.
This would result in something "different" but not
necessarily something "good."
By milling
the Twangcaster bridge from one common (contiguous) piece
of material, string vibration travels without interruption throughout
the bridge and into the guitar.
In this
photo you can see the large chunks (identified with the black
hashmarks) that will be removed.
|
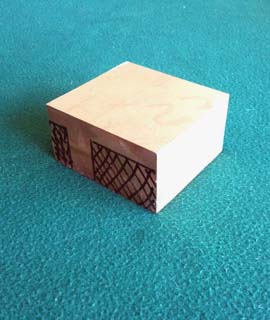
|
|
|
|
|
Here
you can see the top portion has been milled away. It's starting
to look like a bridge. |
|
|
|
|
|
Making
the Twangcaster bridge is a slow and precise process.
We will spend more than one hour per bridge in just the milling
operation. From there it goes to deburring, cleanup, polishing,
and then on to plating. This photo shows the milling process
of the bridge underside.
A perfectly
flat bridge mated to a perfectly flat guitar top results in
the optimum method of transferring vibration from the strings
to the body. Although stamping out a bridge from cold-rolled
steel is acceptable, it is not superior. To ensure a perfect
mating, the bridge base plate must be milled.
At this
point you're probably thinking, "If this is so good, why
didn't Leo Fender do this?" The fact is, traditional bridges
were not designed to be "tone improvement" devices.
They were designed as a method of anchoring strings and/or to
provide a method to pivot the strings as with a tremolo. Don't
agree? Then take some time to research bridge patents and see
how many you can find that make the claim to affect or improve
tone.
|
|
|
|
|
|
Here are
two completed bridges. The one on the left is for the guitar
that does not install a pickup in the bridge. It is ideal for
a guitar with a humbucker in the bridge position. The bridge
on the right is for our traditional Twangcaster guitar
and will fit most Tele ®-style guitars.
Tele®
is a registered trademark of FMIC
|
|
|
|
|
|
The
following photos show the standard installation of the Twangcaster
bridge. Notice the tone chamber that is routed in the guitar body
just behind the bridge pickup cavity. |
|
|
|
|
|
This
is a view of the underside surface of the Twangcaster bridge. |
|
|
|
|
|
Underside
view of the Twangcaster bridge with a Lindy Fralin "Blues
Special for Tele" pickup.
|
|
|
|
|
|
The Twangcaster
guitar uses machine screws and brass inserts to mount the bridge
to the guitar surface. This is far superior to wood screws found
on all other guitars. Notice that the bridge will be screwed
down using four screws at the back and two screws at the front.
If the front
screws were not added, the bridge would rock back, thereby lifting
the front of the bridge off the guitar surface. The front screws
are added to ensure a snug mating of the bridge to the guitar
body which optimizes the transfer of vibration to the guitar
body.
Try this:
Next time you have your T-style guitar out, see if you can slide
a piece of paper under the front edge of your bridge. If the
front of the bridge is not snug against the guitar body, you
are losing tone.
|
|
|
|
|
|
Here
is a nice view that shows the installed bridge on the Twangcaster
guitar surface. Notice the cuts for the wires. These routes are
specially designed to allow the installation and removal of all
electronics without having to break a solder. |
|
|
|
|
|
The completed
install.
Again, thank
you for taking the time to learn more about my Twangcaster
guitar and innovative bridge design. If you have any questions
or comments, please don't hesitate to drop me an e-mail or give
me a call.
~ Lloyd
Prins
|
|
|
|
|
|